The plastic injection molding machine is molding equipment that processes various thermoplastics or thermosetting plastics into various shapes of plastic products through molding dies. Plastic injection molding machines have a very wide range of applications. The equipment currently has a very wide range of applications in the automotive industry, daily necessities, construction, 3C industry, industry, pipe fittings, medical and other fields. YG plastic injection molding machine manufacturers have provided customers with injection molding turnkey projects for a variety of products. In addition, YG manufacturers also offer a variety of molds for injection molded parts. If you want to make injection molded parts, please contact us for injection molding solutions.
Application of Plastic injection molding machine
Daily necessities
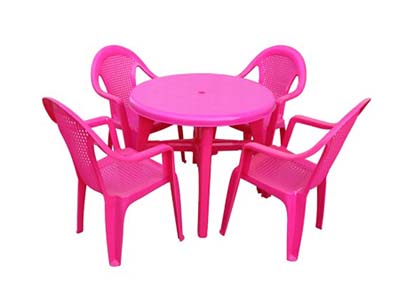
- Plastic chairs
- Plastic Toy
- Plastic tables
- Plastic tubes
- plastic tableware
- Rain boots
Automotive industry
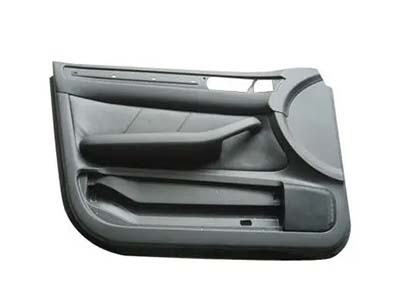
- automotive exterior parts
- automotive interior parts
- automotive lighting systems
Home appliances
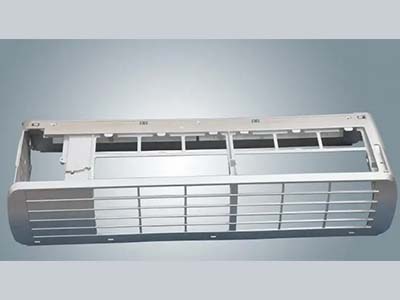
- air conditioners
- washing machines
- refrigerators
- TV sets
Industry
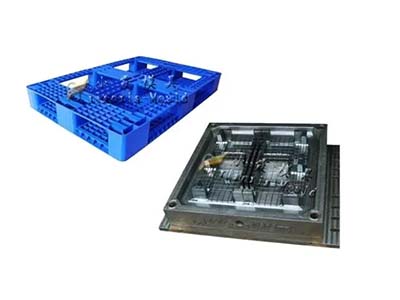
- turnover boxes
- Plastic pallets
- industrial trash cans
- large plastic parts molding
Medical
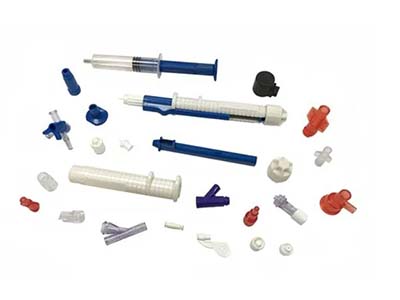
- syringe
- test tube
Pipe fittings
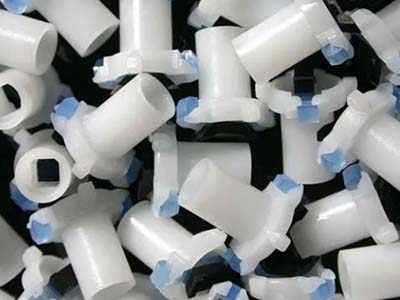
- PP pipe fittings
- PVC pipe fittings
- PPR pipe fittings
- special pipe fittings
Plastic Injection Molding Machine Classification
According to different classification standards, there are various types of injection molding machines.
- According to the plasticizing method, there are plunger-type and screw-type injection molding machines.
- According to the power source of the injection machine, there are mechanical, hydraulic, pneumatic, and electric injection molding machines.
- There are single-color machines, double-color machines, and multi-color machines according to the number of barrels.
- According to the arrangement of injection and lock devices, there are vertical, horizontal, vertical compound, angle, and multi-mode rotary injection molding machines.
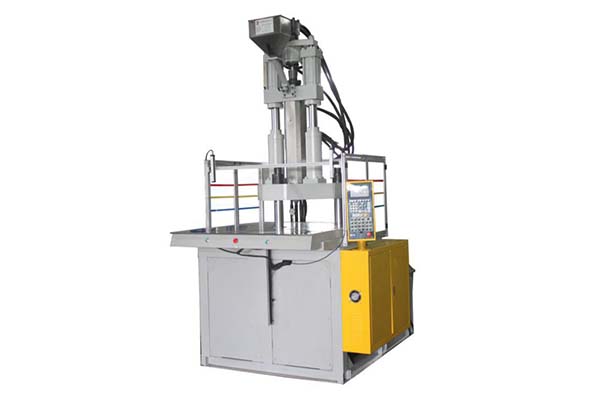
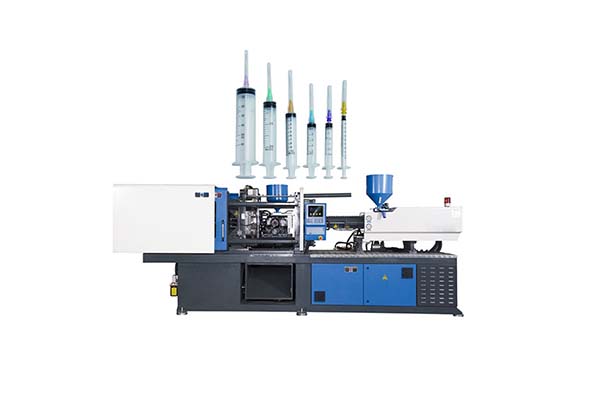
Although there are various types of injection molding machines, you can tell us your needs and we will recommend suitable equipment for you according to your needs.
Injection Molding Machine Components
Although there are many types of injection molding machines, they are generally composed of the following four parts. They include four parts: clamping device, injection device, drive device, and control system.
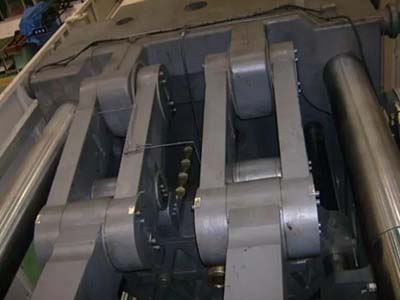
Clamping Device
The clamping device of the injection molding machine ensures the clamping, opening, and ejection of the product. At the same time, the mold clamping device ensures that the mold has enough clamping force to resist the pressure caused by the molten plastic entering the mold cavity, so as to prevent the bad state of the product caused by the mold Dalai Lama.
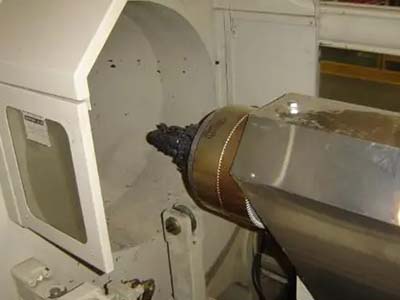
Injection Device
The injection device is the most important part of the injection molding equipment. Its function is to melt the plastic in the injection mold cavity through the screw under specific pressure and speed.
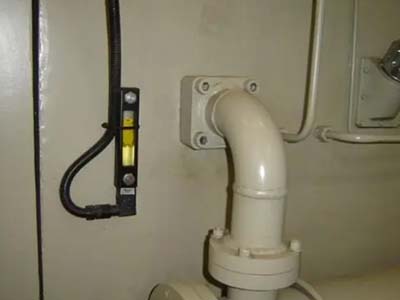
Drive Device
The driving device is mainly a hydraulic transmission system, which is composed of various hydraulic components and auxiliary components. Its function is to provide power to the injection molding machine according to various actions required in the molding process to meet the pressure, speed, temperature, and other requirements required by the injection molded parts.
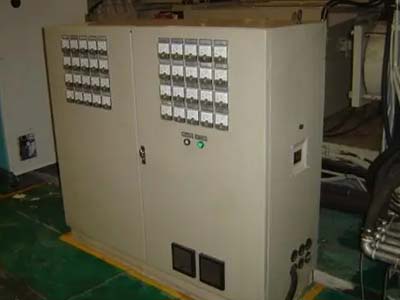
Electrical Control Device
The electrical control device is the device that provides power to the plastic injection molding machine. It can realize the coordinated operation of the electronic control system and the hydraulic system, so as to meet the process requirements such as pressure, temperature, and speed required for injection molding.
The Working Principle of Injection Molding Machine
The injection molding machine uses the push of the screw to heat the raw material, and the plastic is melted in a flowing state and injected into the closed mold core. Driven by the screw or plunger of the injection molding machine, the injection system of the nozzle and the mold enters the mold cavity. The molten plastic is shaped by the mold, then cooled and dried, and the injection molded parts can be obtained from the mold.
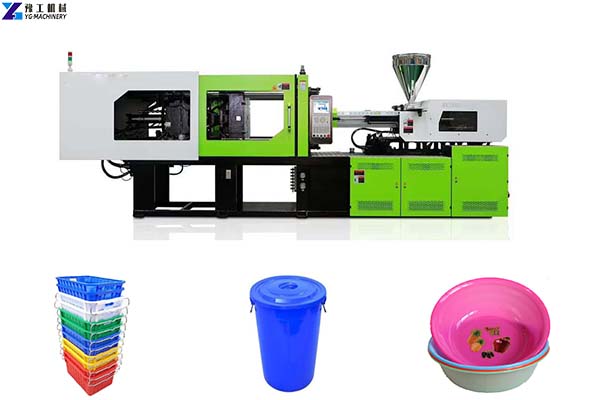
Injection Molding Process
The injection molding process of plastic parts mainly includes 6 stages: mold clamping, filling (gas-assisted, water-assisted) pressure holding, cooling, mold opening, and demolding.
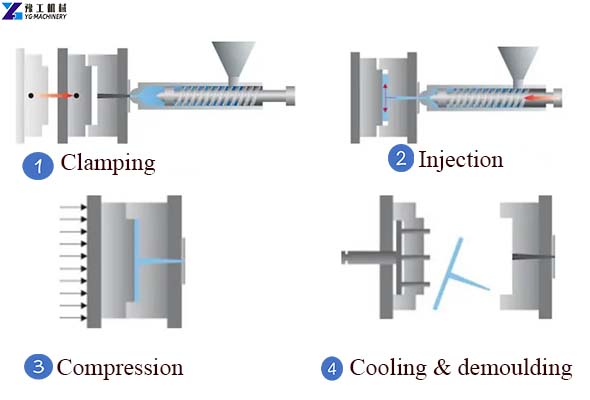
- Close the mold and begin injection molding until the mold cavity is more than approximately 95% filled.
- Under the action of the holding pressure, the melt in the cavity is fed due to cooling, and the product is compressed and densified.
- Driven by pressure, the plastic melt enters the vertical runner, main runner, and branch runner of the mold through the nozzle of the injection molding machine, and then enters the mold cavity through the gate.
- After mold opening and demoulding, you obtain the injection molded plastic parts.
YG Plastic Injection Molding Machine Features
- Various shapes
Make plastic products with complex shapes
- High Quality
The product is in good shape and the quality is guaranteed.
- Standardize
Standardize, standardize, and serialize injection plastic parts
- Simple Operation
Simple operation and easy replacement of forming molds.
- Various models
A variety of injection molding machines are available to meet the various needs of customers
- Customized Mold
YG provides injection molds that can be customized for a variety of complex shapes.