PS foam food box machine uses PS material sheets to make foam food containers. By changing different molds, the equipment can be used to produce fast food boxes, foamed dishes, trays, and other containers. PS foam food container production line mainly includes foam sheet unit, vacuum forming machine, plastic crusher, recycling line, and other equipment. In addition, YG also provides a variety of food container-making machines such as aluminum foil container machines, paper bowl machines, paper cup machines, plastic bowl lid making machines, etc. If you are interested in these food container-making machines, please contact us.
Finished PS Foam Container Display
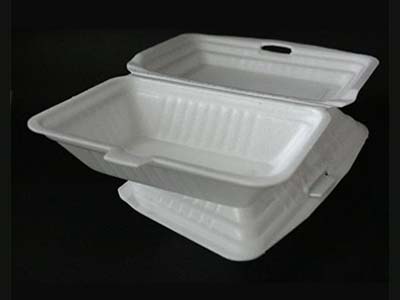
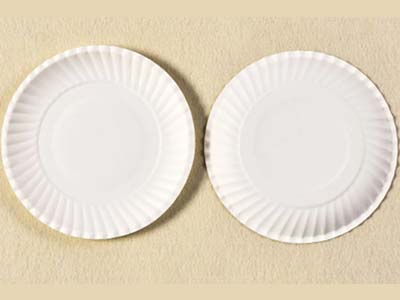
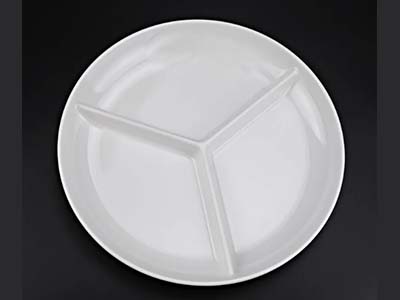
About the Foam Lunch Box
Foam lunch box refers to tableware made of disposable expanded polystyrene plastic. The foam lunch box has the characteristics of oil resistance, water resistance, corrosion resistance, heat preservation, and heat insulation. The polystyrene plastic pellets and the blowing agent are heated together, the plastic pellets become soft, and the volume expands up to 40 times at the same time. The expanded polystyrene plastic is cooled, reheated, and shaped using molds to become lunch boxes, plastic cups, plastic dishes, and other products. An expanded polystyrene product weighs 30 times less than a regular polystyrene product of the same size. Therefore, the cost of using expanded polystyrene to make lunch boxes is greatly reduced.
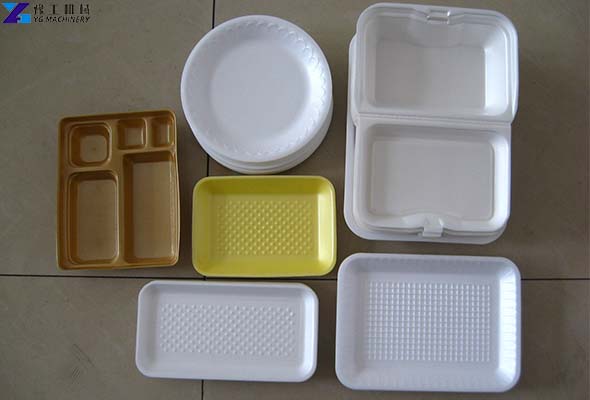
PS Foam Takeaway Box Production Line
YG disposable takeaway box production line has two types semi-automatic and fully automatic. The semi-automatic lunch box production line consists of four pieces of equipment: PS foam sheet unit, automatic vacuum forming machine, pulverizer, and recycling granulator. The semi-automatic production line adds a blanking machine.
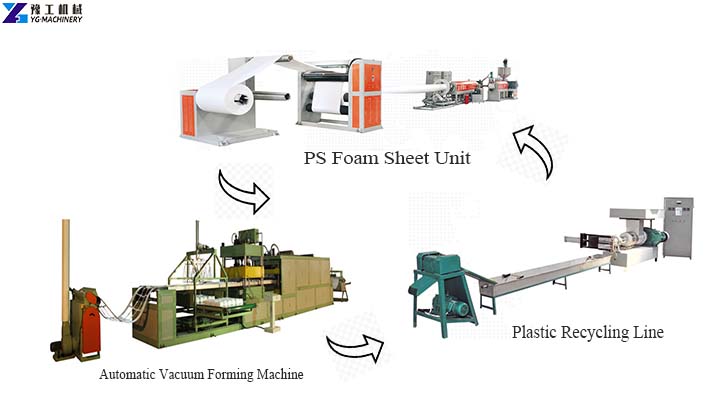
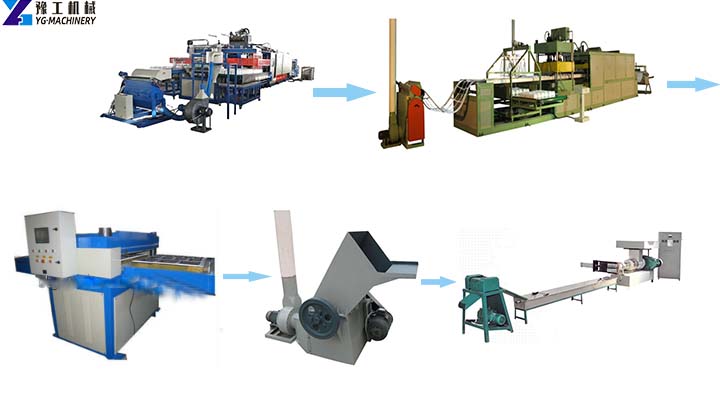
How is Takeaway Container Made?
First, use a PS sheet machine to process polystyrene particles into sheet rolls. Then place the roll of sheet material on a vacuum forming machine to form. The vacuum forming machine rolls the sheet material into foamed containers mainly through a die. The remaining scraps can be pulverized by the pulverizer and then sent to the granulating unit for recycling.
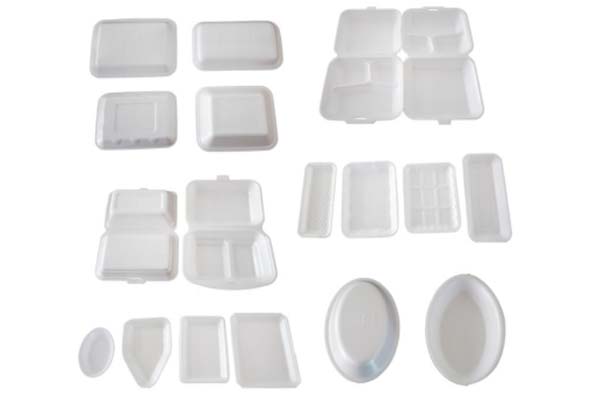
Main PS Foam Food Box Machine Introduction
PS Foam Sheet Unit
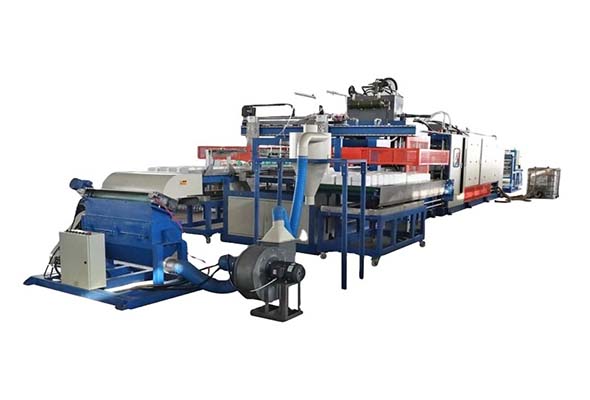
The foam sheet unit adopts the double machine series high foam sheet production process. Adding a blowing agent during the extrusion of polystyrene raw materials by using this equipment. After grinding head extrusion, foaming, cooling, shaping, pulling, and winding into the finished sheet. PS foam sheet is a new type of packaging material, which has good thermal insulation and cushioning properties and also has a pearl-like appearance and color. After vacuum forming, the PS foam sheet is made into various types of food containers such as lunch boxes, trays, dishes, etc.
Parameter | Unit | YG-75/90 | YG-105/120 | YG-110/130 | YG-135/150 |
Capacity | kg/h | 80-100 | 200-240 | 230-260 | 280-360 |
Sheet thickness | mm | 1–4 | 1–4 | 1.5–5 | 2–5 |
Sheet width | mm | 640-1080 | 640-1080 | 800-1080 | 900-1080 |
Cutting method | single cutting | single cutting | single cutting | single cutting | |
Cooling method | wind&water cooling | wind&water cooling | wind&water cooling | wind&water cooling | |
Foaming rate | 10–22 | 10–22 | 10–22 | 10–22 | |
Butanegas pressure | Mpa | 0.9-1.2 | 0.9-1.2 | 0.9-1.2 | 0.9-1.2 |
Installation power | kw | 160 | 180 | 240 | 320 |
Installation Dimension | m | 24x6x3 | 30x6x3 | 32x6x3 | 35x8x3 |
Power supply | 3Phase380V50HZ | 3Phase380V50HZ | 3Phase380V50HZ | 3Phase380V50HZ |
Fully Automatic Vacuum Forming Machine
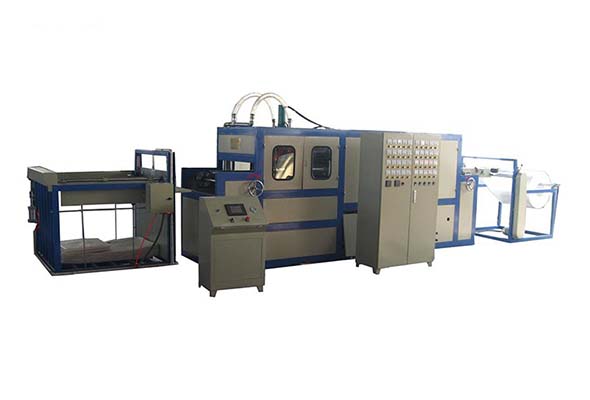
The automatic vacuum forming machine is a new type of thermoforming unit that integrates and cuts. This fully automatic vacuum forming machine is used in the fully automatic PS foamed lunch box production line. The semi-automatic vacuum forming machine does not have the function of cutting. The automatic vacuum forming machine adopts the man-machine interface computer touch screen control system, which is easy to operate. It has the characteristics of large forming area, convenient cutting and fast forming speed. The equipment can be used to produce a wide variety of shaped sheets. The shape of the finished product can be achieved by changing the mold.
Parameter | Unit | YG-1100 | YG-1250 | YG-1400 |
Forming area | mm2 | 1100×1100 | 1100×1250 | 1100×1400 |
Cutting height | mm | 160 | 160 | 160 |
Production efficiency | Die/S | 3-4 | 3-4 | 3-4 |
Installation dimension | m | 19x6x3 | 21x6x3 | 24x6x3 |
Installation power | kw | 160 | 180 | 200 |
Power supply | 3 Phase 380V 50HZ | 3 Phase 380V 50HZ | 3 Phase 380V 50HZ |
Plastic Shredder
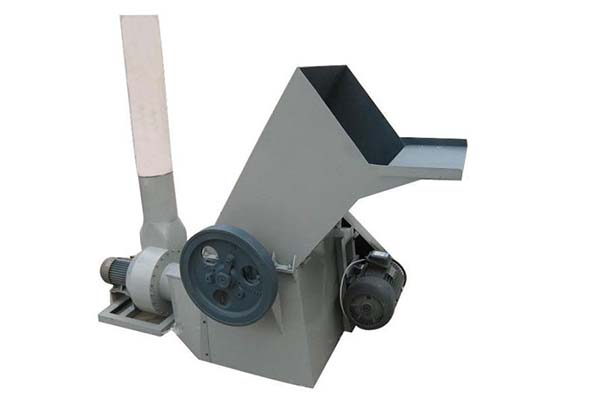
This plastic pulverizer is specially used for pulverizing foamed plastics. The ability to crush polystyrene foam is strong and the efficiency is high. In the PS foam lunch box production line, there is cutting of leftover and unused materials. Therefore, it needs to be pulverized by a plastic pulverizer and then put into a granulator for recycling.
Circulating Pelletizing Line
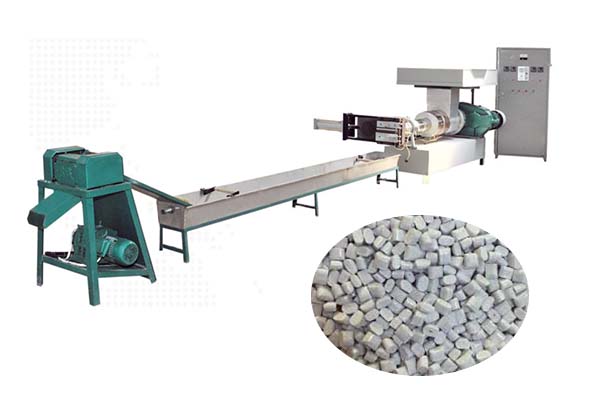
The plastic granulation recycling line is used for the recycling and granulation of high-expanded polystyrene products. The recycling granulation production line mainly includes screening, feeding, extrusion, cooling, pulling, air drying, dicing, packaging, and other processes. Plastic pellets produced by recycling granulation can be recycled to reduce waste.
Model | YG-105 |
Screw diameter | 105mm |
Dimension | 8x3x2m |
Weight | 1.5t |
Power supply | 3 Phase 380V 50HZ 3Phase 220V 60HZ |
Features of PS Foam Food Box Machine
- Since it uses foam material, the production cost of each lunch box is lower than that of ordinary lunch boxes.
- The mold can be replaced and customized.
- This PS foamed lunch box production line can be used to produce takeaway lunch boxes, dishes, trays, and other foamed containers
- All PS foam food box machines feature high output, stable performance, and high product quality.
- The production speed of the automatic vacuum forming machine is fast, the power consumption is low, and the proportion of waste is small.
- The blanking station moves along with the motor, which is conducive to changing the mold and saves time for mold replacement.